For All
Dairy Farmers & Dairy Service Technicians ...
Dont
Spend $1000's Replacing Faulty Electronics In Your Dairy ...
Until You've Read These Pages
Boumatic
As you can read on our ‘About
Us’
page ... Boumatic 4600
Signature Series Detachers
... or ‘automatic cup remover’ boards ...
were
where we first started with dairy circuit board repairs.
Having
focused on them for a number of years ... we've now
became
inundated with other models from Boumatic's range ...
as
well as many other brands.
Detachers
ParlorMetrix Detachers
These are the latest of the Boumatic boards we've been asked to repair
... the ParlorMetrix detacher units.
ParlorMetrix
detachers consist of two boards permanently connected and sandwiched
together on a small metal frame ... there's one needed for
each milking point
ParlorMetrix detachers
form a fairly sophisticated system that monitor the milking process
... operator and equipment wise ... and in the
words of Boumatic's marketing people, are a ... "
performance-monitoring
network of detachers that transmit data to a PC to provide information
that can be used to maximise parlor productivity and profitability"
Download pdf brochure
here ...
One
way they do this is through some fairly unique bar graphs and charts
generated for each milking, to show at a glance how well the session
went.
This then enables fine tuning of procedures and detacher
settings etc. to get the best out of the milkers, the cows and the
dairy.
Another feature is the fact that the system has been
designed for the detachers to be mounted remotely to each milking
point, ie in a well sealed box in an adjacent room to the main dairy
... which protects them enormously from the hostile
environment that detachers normally operate in.
Despite all this, electronics being electronics, a certain percentage
are still going to break down.
That is where we can help, and can
save you a substantial
amount of money and aggravation over buying replacements.
Contact us if you have any questions about fixing any of these boards.
Components
are getting smaller and smaller ... despite it's tiny size,
the diode array at the end of this tooth pick, has six legs.
This
one 'fell' off as we attempted to connect to it to measure it's
operation ... try stitching one of these little suckers
back on if you want to check your eyesight or your soldering skills !!!
The
3200 Series Detachers
- Have
you
been having trouble with the switches on your 3200 detachers?
- Water
getting in and rusting them out?
- Don’t
really want to spend big money fitting stainless steel ‘piezo’ switches?
Well
... we can replace them with genuine switches
... the same as the originals ...
which will give new life to your boards.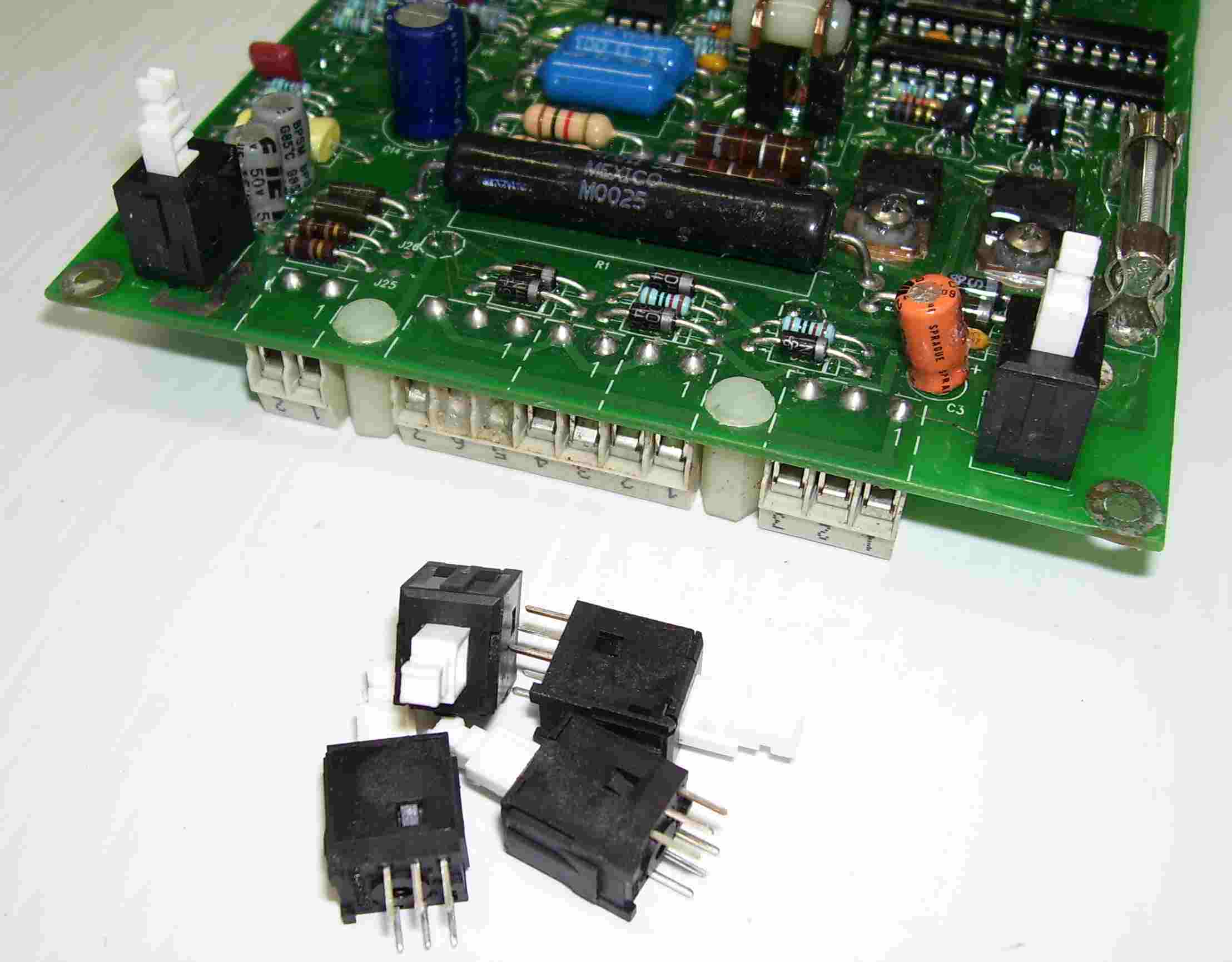
... and
an advantage (over stainless switches) ... is that
each
detacher can still be ‘reset’ from the front panel ...
rather than having to get in to disconnect the power, every
time a reset is needed.
If you have one or more
faulty boards ... contact us ...
we’ll organise
a time that suits us both ... then send in the
boards for a
prompt repair and quick turn-around time.
If there is a
possibility you may be interested in fitting stainless switches some
time in the future ... we also fit flyleads to the
board at
the same time ... so that you
can fit the switches yourself any time you choose ...
without having
to send the boards off again ... and
I’m sure more importantly for you ... not having to
take them out of the dairy again..
If
for some reason you’d rather not have these flyleads fitted
...
please mention that when organising the work to be done.
For those of you who don’t know what is involved in fitting the
stainless piezo switches ... it entails (once the above
mentioned flyleads are added)
...
... removing the front cover
... carefully pulling the shaft out of the pcb switches with a pair of
pliers
... fitting the new switches in place of the original buttons
... then hooking up the wires from the new switches to the flylead
connectors mentioned above
Really quite simple ...
Also,
we should add too ... that obviously other faults
can occur on
these boards as well ... so it’s not always the
switches. Feel
free to contact us if you have any questions about these boards.
If
you are sending in any of these boards ... please
download
and print out a Repair
Form ...
fill it in ...
and send it with your boards. It provides us with information
about the symptons of the fault you're seeing ... shipping
... and your preferred payment method.
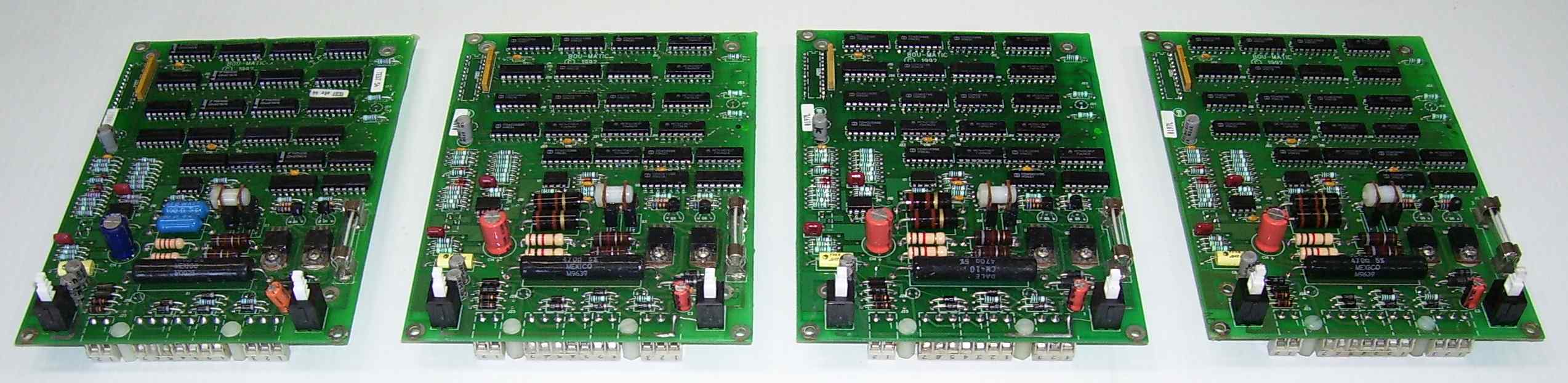
Another
batch of 3200 Detachers with new switches
3400
Perfection Milk Meter Detachers
These are more sophisticated again ...
than the 3200 series detachers.
They
include quite a bit more intelligence ... along
with digital displays to provide data at each milking bay
... as well as a communications channel to and from
the
computer back in the office.
As with most dairy equipment
... moisture is probably the biggest killer for
these
boards. It then depends on where that moisture ‘sits’ and where the
moisture protection barrier is weakest or has broken down ...
as to what fails ... and what symptons
you will have.
We
have seen everything from plain corrosion ... of
tracks and leads ... failed
seven-segment displays ... faulty IC’s
...
through to failed microprocessors.
So far most have been repairable ... so don’t write
yours off yet.
It's
hard to give a firm price for repair up front ...
it
depends on where the damage is ... as to what the
end cost
will be.
Obviously ... replacing an 80 pin surface-mount
microprocessor ... or all
twelve
seven-segment displays, is more time consuming and
expensive ... parts wise ...
than a simple
corrosion repair job.
If
you are sending in any of these boards ... please
download
and print out a Repair
Form ...
fill it in ...
and send it in with your boards. It provides us with
information
about the symptons of the fault you are seeing with the board
...
and shipping and payment options.
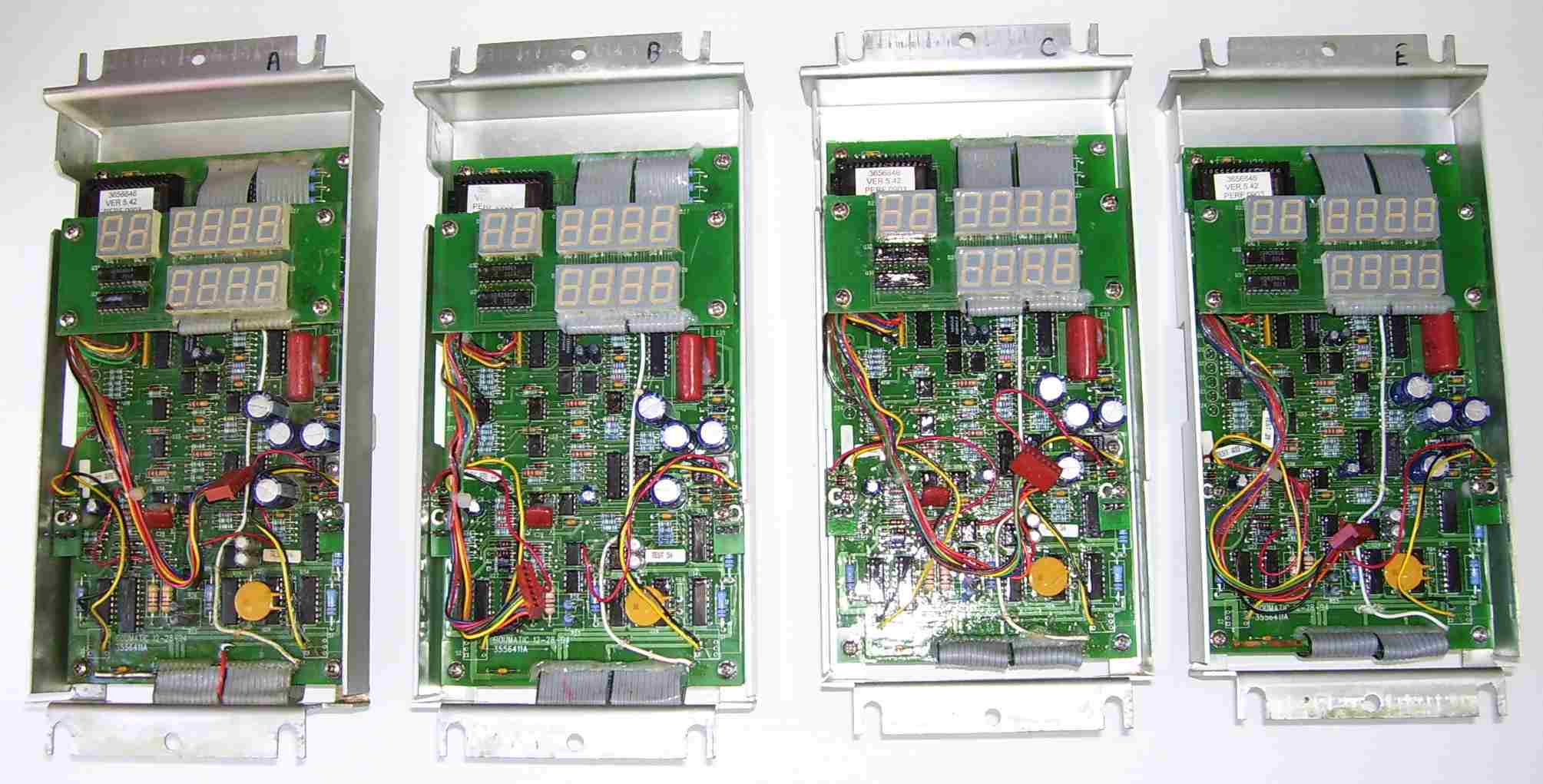
Some
more 3400 detachers
4600
Signature Series Detachers
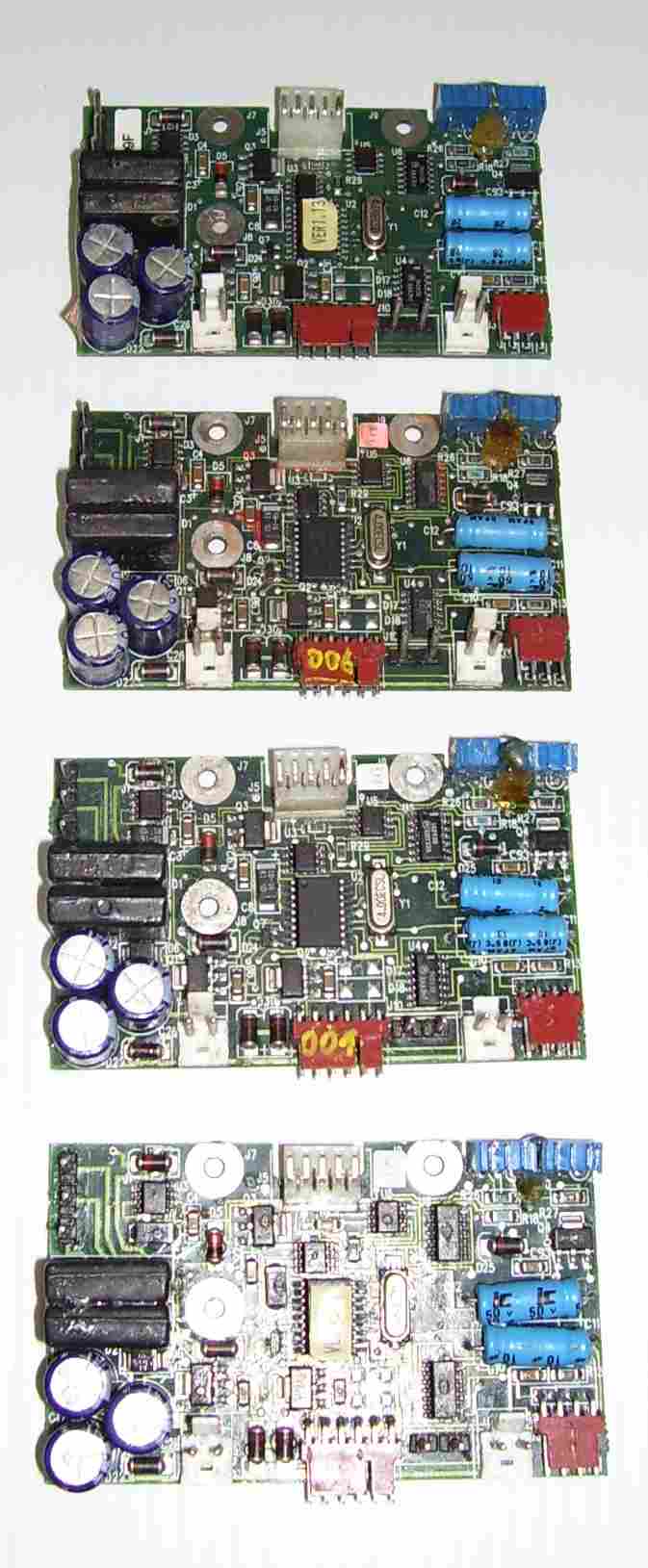
As
mentioned above, these boards are the ones we cut our teeth on
... and again ... moisture
seems to be the main
cause of their problems.
The sort of faults we see are ...
corrosion of tracks and connectors ...
faulty pots
... blown surface mount led’s, mosfets and IC’s
...
and also the occasional ‘misfiring’ or dead microprocessor.
We
keep a full series of parts for these boards ... so
most
faults are fixable. Our main weapon is a sophisticated test jig that we
designed and built to put the boards through their paces ...
initially to find faults ... and then to
test them
thoroughly after repair.
If you are sending in any of these boards
... please download and print out a Repair
Form ...
fill it in ... and attach it to your
boards. It
provides details of the fault you're seeing ... and
shipping
and payment details.
If you'd like us to program the boards with your
settings before we send them back ... please
download and fill in this form also.
Feel free to contact us with any questions you may have.
4600 Detacher
...
front and rear views
Pulsation Controllers
PC-201
Pulsation Controller
These
older boards do an amazing amount of work over their lives
...
so it is not surprising to see them fail occasionally.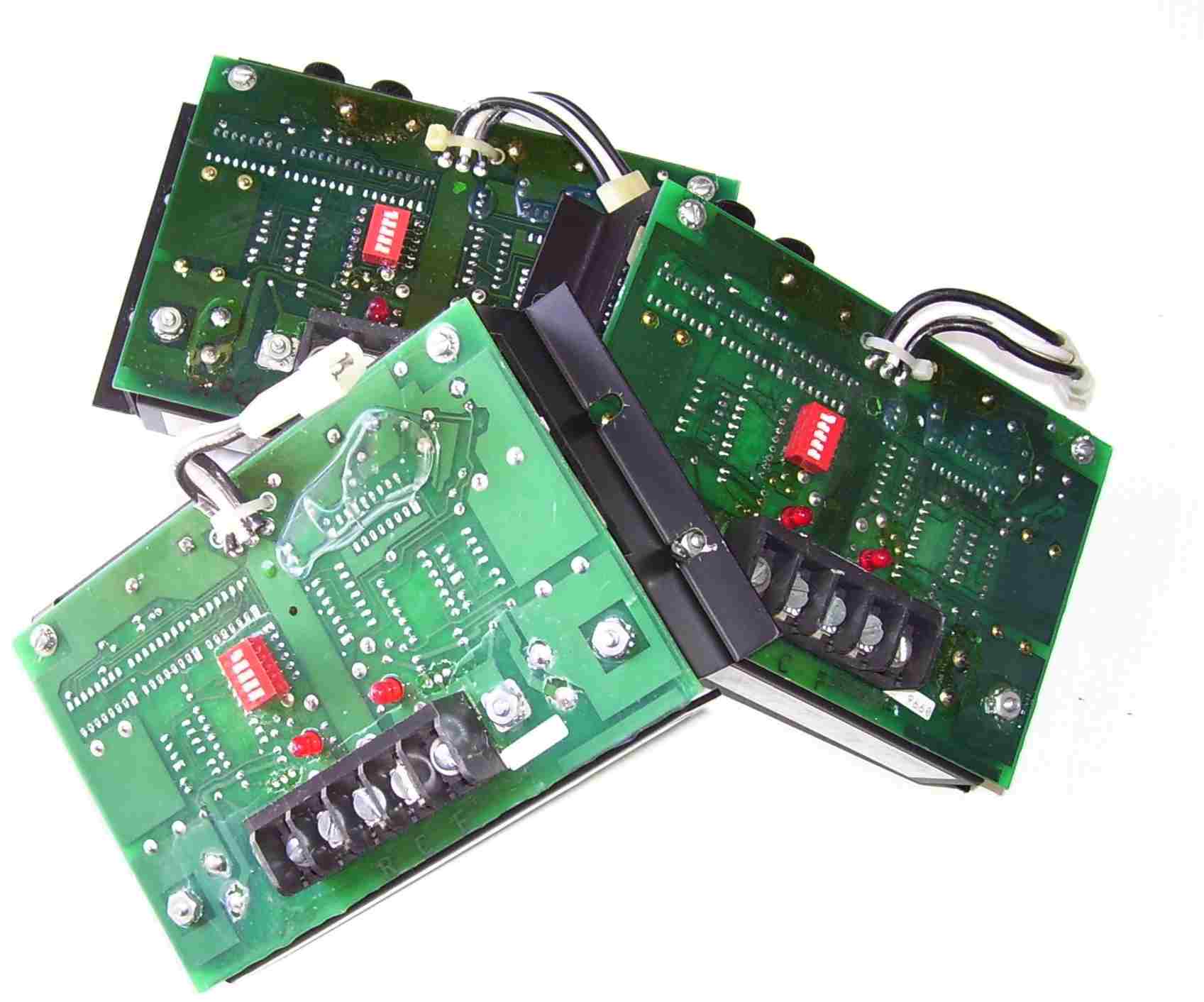
Having
said that ... on most of the ones we see
...
the faults are caused by wiring or external factors
...
not by any inherent weakness of the board itself.
Most
times the repair entails replacing the power transistors ...
supply diodes ... power resistors
...
driver transistors, and repairing burnt tracks etc
...
then sealing the pcb ... and we also fit
a pair of
fuseholders to add protection from the external factors mentioned above.
As
long as no-one fits fencing wire in place of the fuses ...
the additional protection will pay off handsomely if anything
major goes wrong externally.
If
you are sending in any of these boards ... once
again
... please download and print out a Repair
Form
... fill it in ... and attach
it to your
boards. It provides details about the fault ... and
details
about payment and shipping.
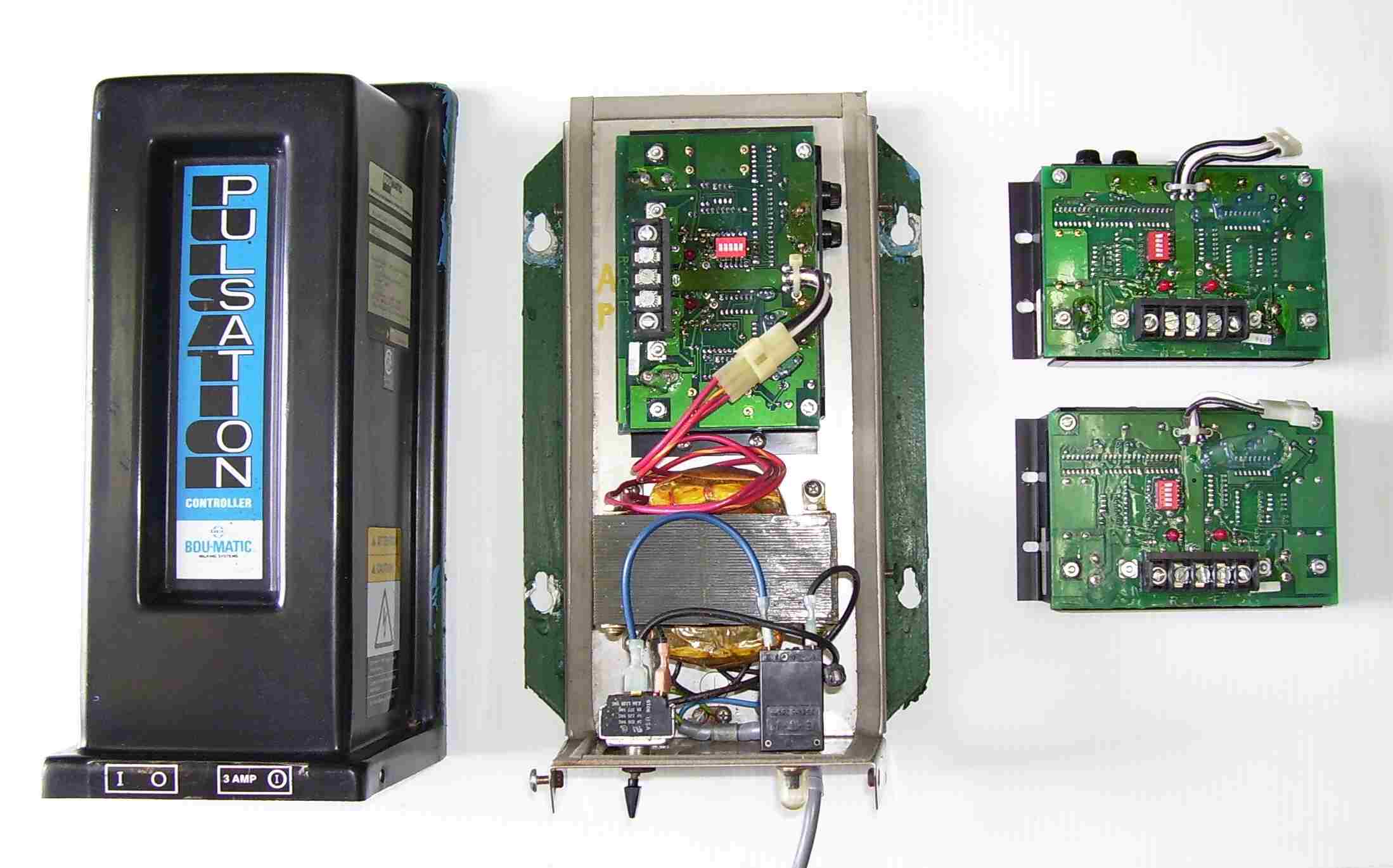
PC-201
Pulsation Controller with Power Supply and Extra Boards
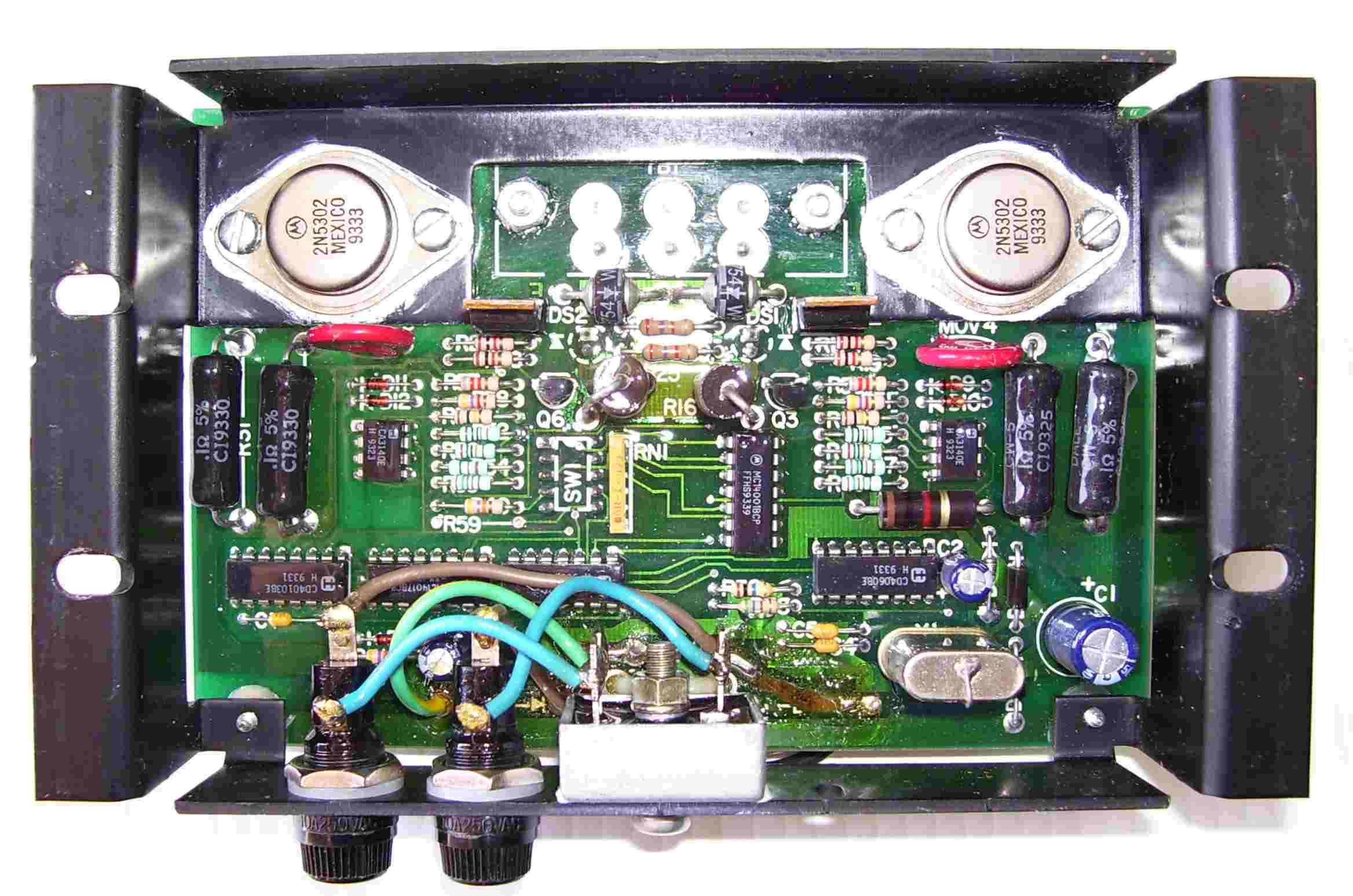
PC-201 ... before ... and after
PRISM
Pulsation Controller
These newer pulsation control boards are a much more sophisticated
update of the PC-201.
They
are programmable ... so it pays to go through the
diagnostic procedure described in the manual before sending any in
... as often they can be set straight by
reprogramming or
resetting in place.
The board pulsation rate and ratio can be set either with the onboard
DIP switches or via
a PC or a Network Controller.
If set via the latter, the settings are retained until reprogrammed
.. but note
... the DIP switches will have no effect unless
the device is re-programmed to allow it.
If
the 'Switch' led is on, the switch settings are adjustable
...
but if 'off', the board can only be adjusted by programming.
If you aren’t sure about the troubleshooting procedure or
need the instructions ... download them here
...
or give us a call and we should be able to help you out.
If
you are sending in any of these boards ... please
download
and print out a Repair
Form ...
fill it in ...
and attach it to your boards. Again ...
it provides
details for payment, shipping and the fault you are having
with the board.
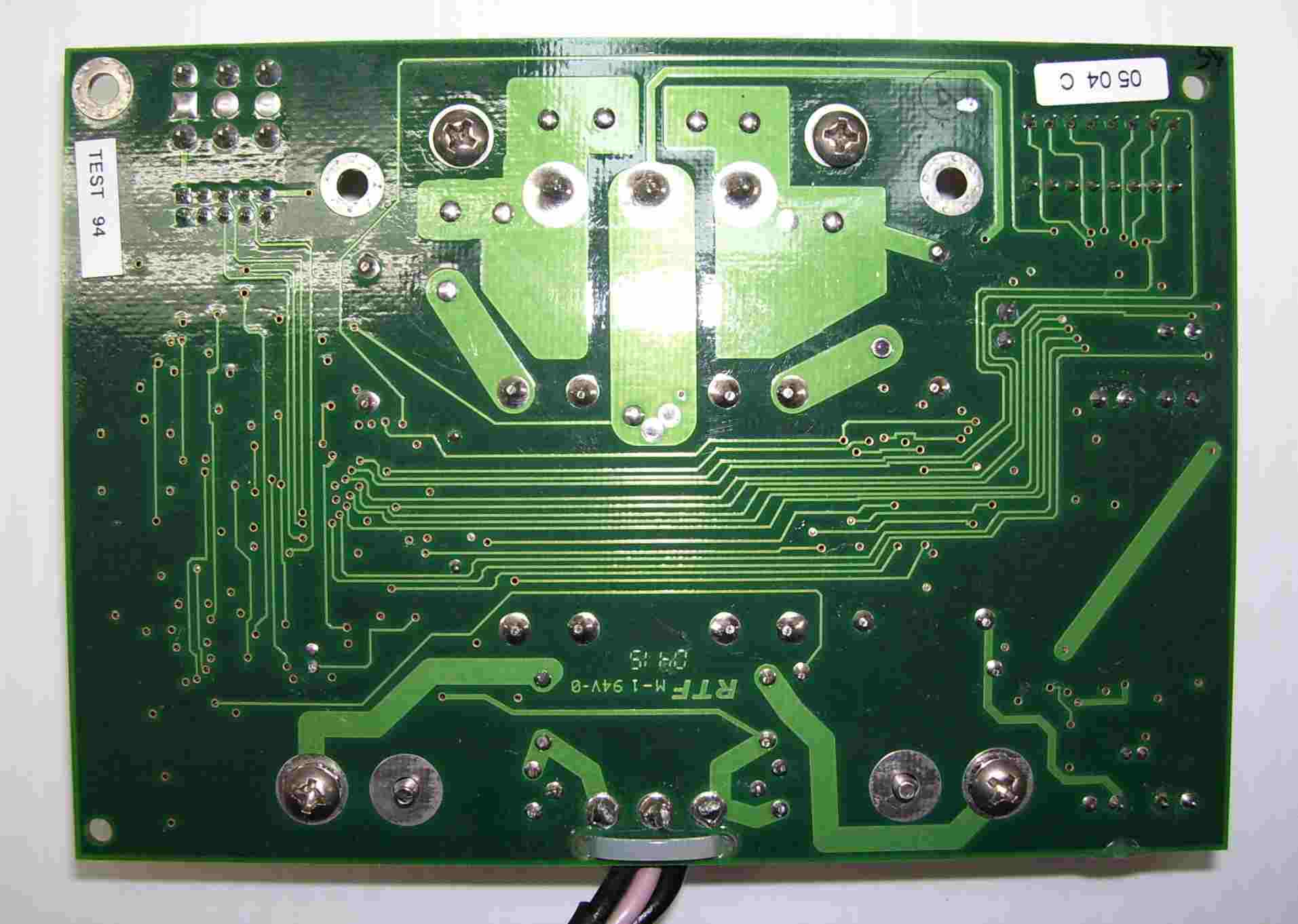
PRISM
PCB ... front and rear view
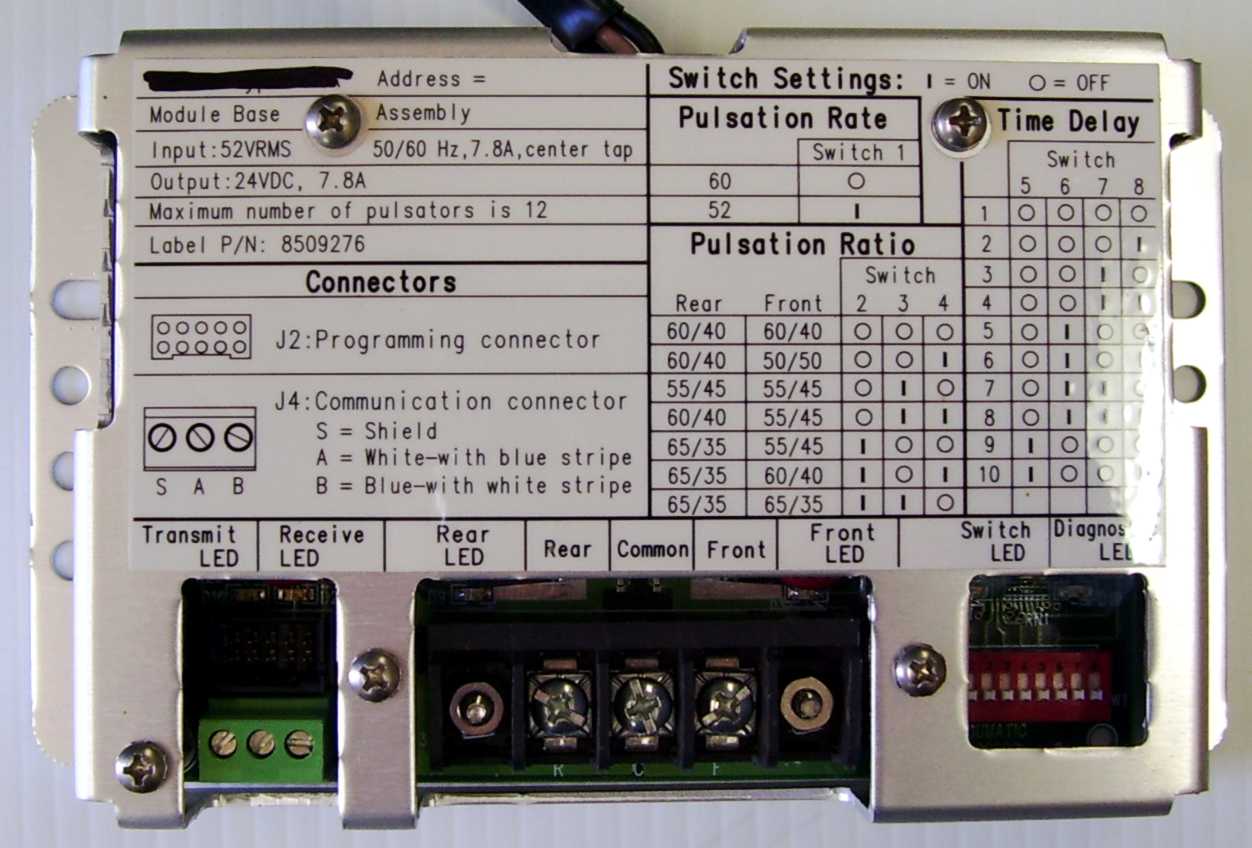
...
and back in it's box
Guardian II
Pipeline Washer
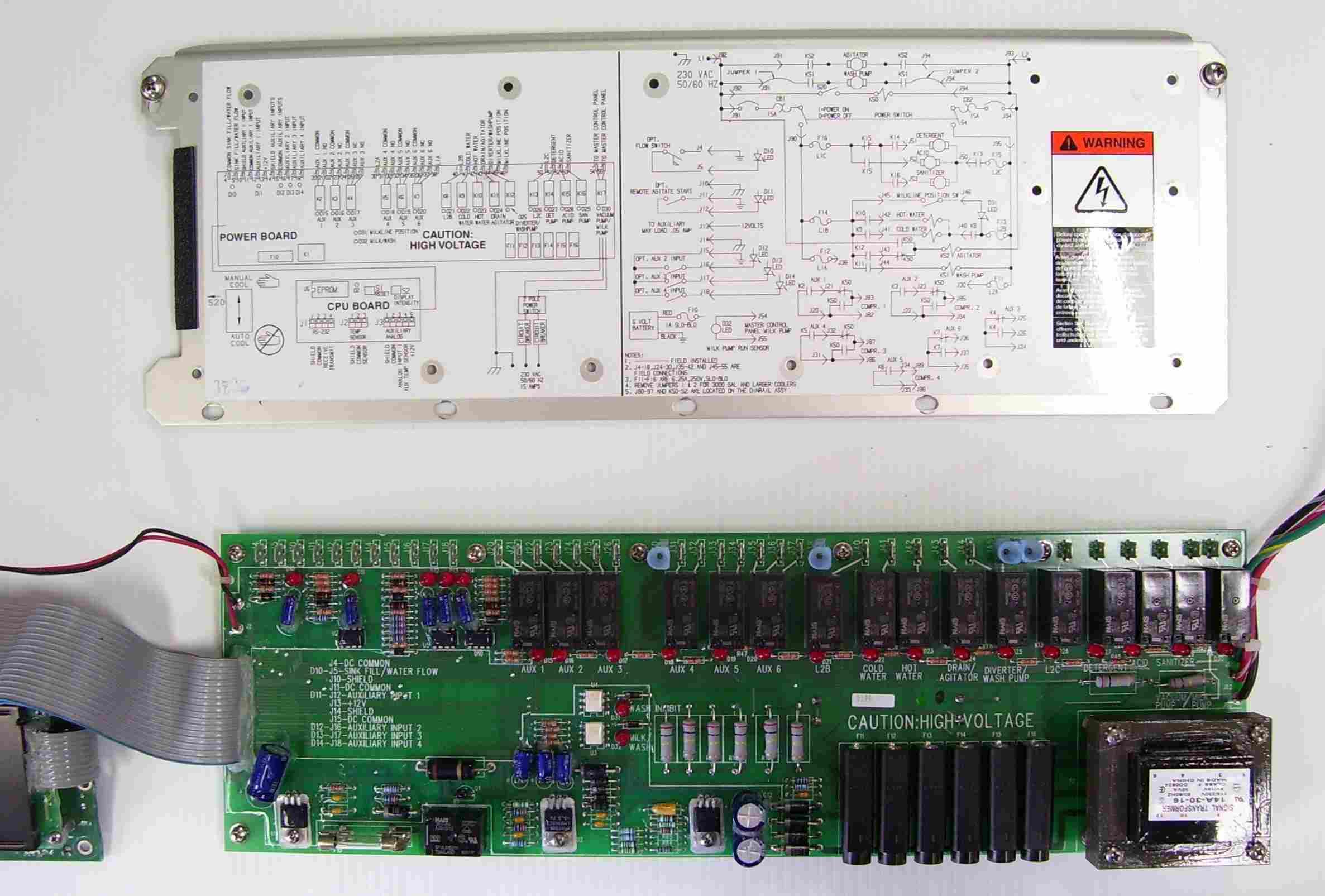
Guardian-II
Control PCB and Mounting Plate
This device is a programmable electronic milk-pipeline washer
consisting of 2 modules.
It
has one module for the control electronics ... the
digital
display screen ... and the programming buttons
...
...
and
the other ... for 3 dosing pumps that are used to
dispense washing chemicals (alkaline, chlorinated, acid) ...
to automatically wash the dairy milk lines.
Of the boards we have seen of this type so far ... Guardian II and Glacier-Guard
... a number have been damaged when they were run
on a generator
... soooo..... if
you ever need to run
your gear on a generator ... make sure the voltage
regulator is set properly ... and dont let it over-rev !!!
If you happen to have a faulty or damaged digital display
... we have located a limited source of
replacements
... so give us a call ... and
we can arrange to
replace it.
We
are also investigating the possibility of providing a back-lit panel,
to light up the display properly ... so if you are
having
trouble reading the LCD panel ... on either the Guardian II
... or the Glacier-Guard ...
contact us for further information.
If you are
sending in any of these boards ... please download
and
print out a Repair
Form ... fill it in ...
and attach it to your boards. It provides details for payment
... shipping ... and details of
the fault you
are seeing with the board.
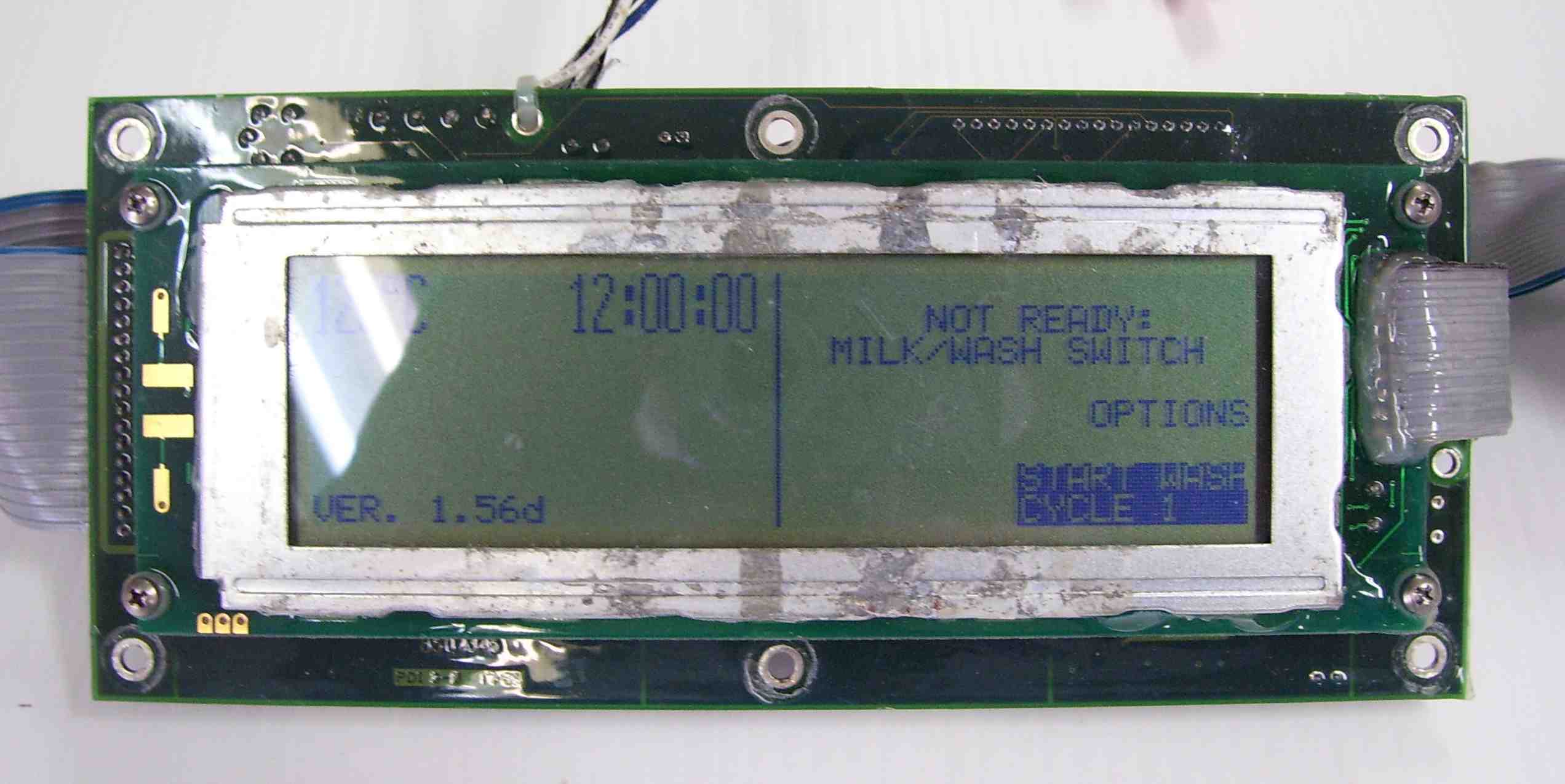
Guardian II Display
Panel
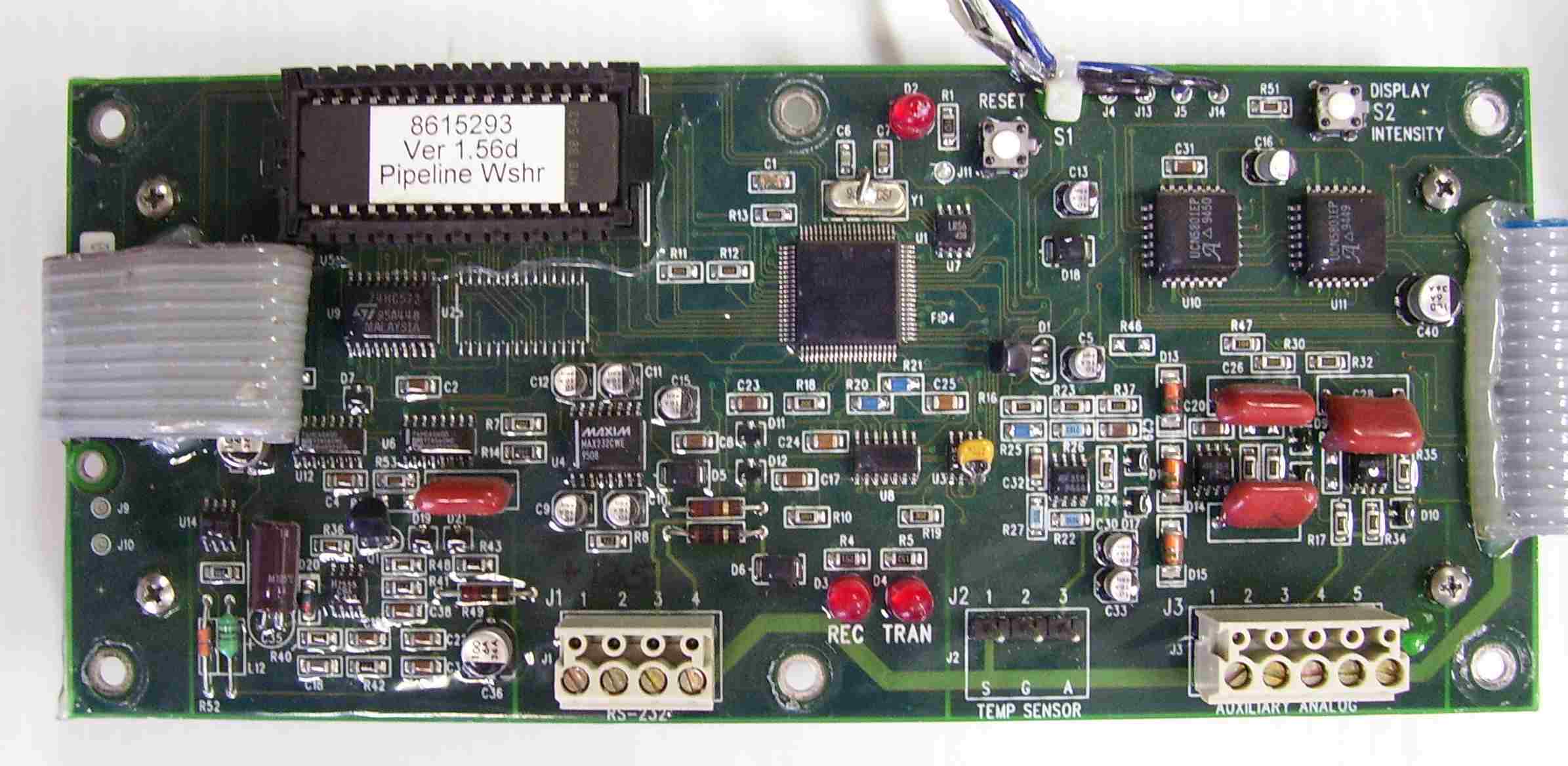
Rear view of Display Panel
Glacier-Guard
Control Board
For
all intents and purposes ... this
board appears identical, cosmetically ...
to
the Guardian II board mentioned above.
The main differences are in it's internal programming ...
and it's end use.
This board is designed to control the cooling of the milk tank
... and also the washing of the same tank.
It
monitors and controls the temperature of the milk ...
running the refrigeration compressors ...
and the
agitator.
Once in the wash cycle ... it controls the
dispensing of chemicals and the washing of the tank.
Regarding
faults with this board, and also LCD panel or
back-lighting problems ... please see the notes on
Guardian
II boards (just above).
If
you are sending in any of these boards ... please
download
and print out a Repair
Form ...
fill it in
... and attach it to your board. Again, it provides
details
of the fault ... and details for payment and
shipping.
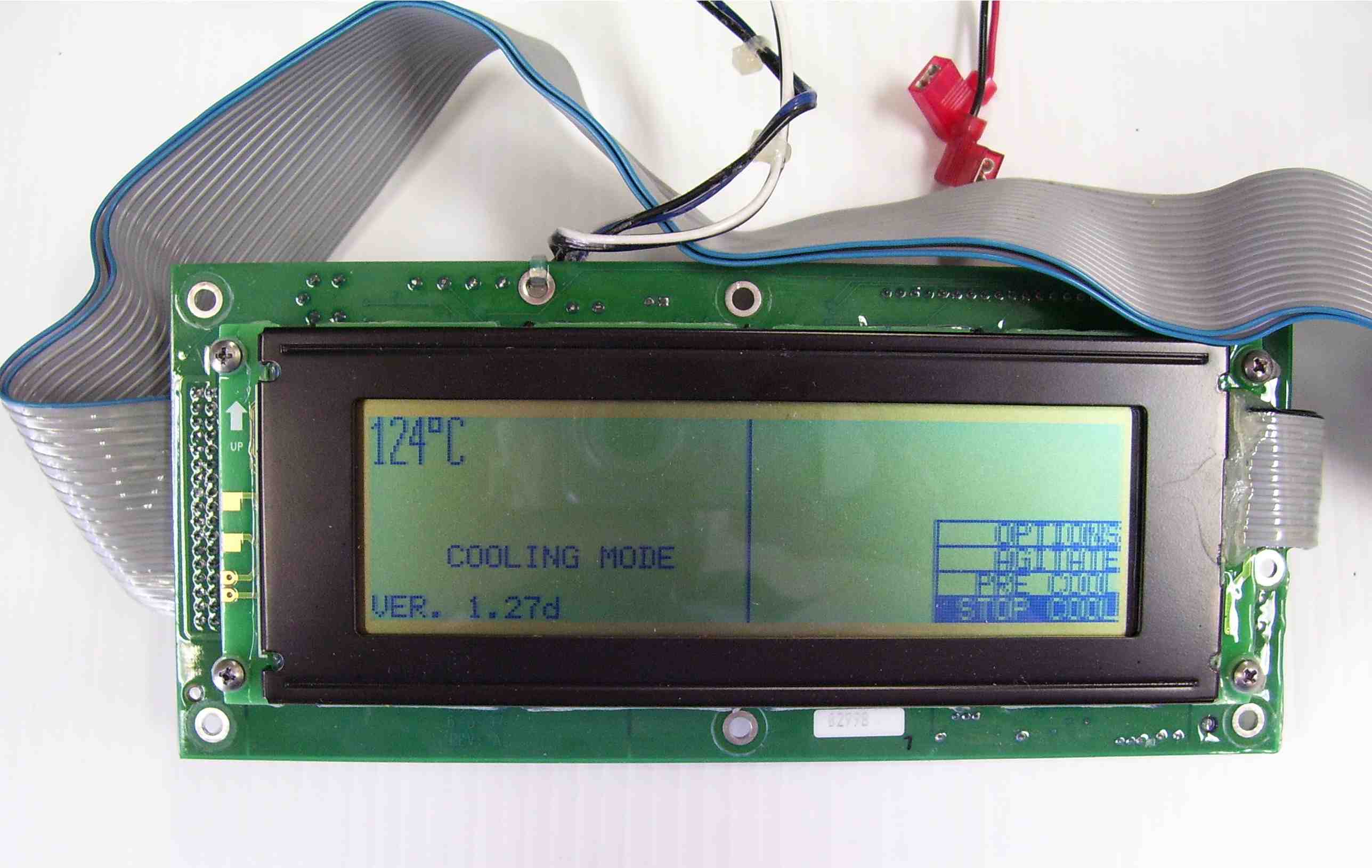
Glacier-Guard Display Panel
ID Controls
...
are Identification
Control
boards
...
just as the name
suggests.
An ID Control in it's stainless
steel box (above)
and 'unwrapped' (below)
They
can be
used in Herrigbone, Parallel, Rotary, Tandem and Swingover
daries.
They
are connected to an antenna ... that
the cows walk
through
or past ... that constantly transmits
power
...
so that any identification neck tag in range (obviously worn
by a
cow) ... will be powered up and will then transmit back it's
own
unique number.
This
allows
data to be collected for each animal,
to be used in the running and managing of the dairy ...
things like milk yield recording, auto feeding, auto drafting
etc
etc.
The
control
boards have been very solidly designed and built
... to be able to run 24 / 7 year after year.
Many
of them have run for 15 years plus. That's not
bad
... try running your truck or your generator for 15
years
straight without a break !!!
...
and if one does fail, it doesn't mean it cant be repaired
and put back into service.
Antenna Drive Transformer and
the section of board it fits onto ...
We
have
repaired enough of these now to be very confident that we will
be able to repair pretty much all that come in.
Several
we
have seen had been damaged by lightning, but were still well
worth repairing and putting back in service.
It's
amazing
that parts are still readily available for these units too, despite
having been built
in the early 90's ... though
not
from
Boumatic I might add.
We
have a 'portal' antenna in the workshop along with a 2050 Network
Controller, which allows us to hook up a complete system and test each
unit fully once we've repaired any faults.
The
ID
controls can then be sent back with confidence knowing they
work the way they are supposed to.
It's
always good to receive this sort of equipment
in batches ... as
setting up the test equipment and going through the test procedures for
each type can be quite time consuming.
Feeder Controls
A
Feeder Control with protective cover removed showing the antenna. The
pcb which is almost the same size, is mounted directly below.
A
pair of cow ID neck tags are resting on top. These are the same tags
used on the rotary platform to 'tell' the system what position it is in
at any given time.
Feeder Control units
are used
to provide feedback to the Network Controller to
identify where the rotary platform is in relation to it's stalls.
The
same ID neck tags that are used for the cows are mounted on the rotary
platform, one ber bail ... and as the platform
rotates, each
tag tells the system where the platform is at any given time.
That
enables an auto feeding system to drop feed into the correct bail
... in
the correct portion size ... for the
specific
cow in the
bail.
As the tags move relatively slowly, and pass within a few centimeters
of the antenna mounted on the front of the feeder
control, the antenna doesn't need to be very large, and in fact is only
about 8" by 10" ... where-as the portal antennas
are about 6'6" high by about 3' wide.
Here
you can see a feeder board that has had some sort of spillage. In the
photo on the left, it has had about half of the rubbish removed.
The photo on the right
(bit out of focus, sorry) shows it all cleaned
up.
It
was only some time later that we discovered that the 'grot' had seeped
in
under all the IC's, so that meant removing all of them !!! and cleaning
up the mess.
2050 Network Controller
The 2050 Network Controller is the
main control unit
for a dairy using the sort of gear shown above ... 3400 or
4600 detachers, Prism pulsation controllers, ID and Feeder controls or
Sort Gate controls etc etc.
All of these devices feed in to it
and provide the information for it to monitor milk yield ...
individual feeding ... cow traffic ...
It
is really just a basic computer ... and is usually
connected to a terminal (screen plus a keyboard) or in some cases a
normal PC ... along with a printer to provide reports.
It
would certainly be regarded as old technology nowadays ...
with it's floppy disks for data storage and back-up ...
but it has proven to be a solid reliable workhorse for many years.
We
have seen several of these which have been repaired ok ...
which was just as well for their owners because a figure of
approx $14,000 was mentioned as a replacement cost ...
A couple of screenshots of a PC
monitoring the 2050.
There's no 'Windows' here
... this is in DOS !!!
Here's an 'interesting' one we
got to work on ... no prizes for guessing what caused this
damage.
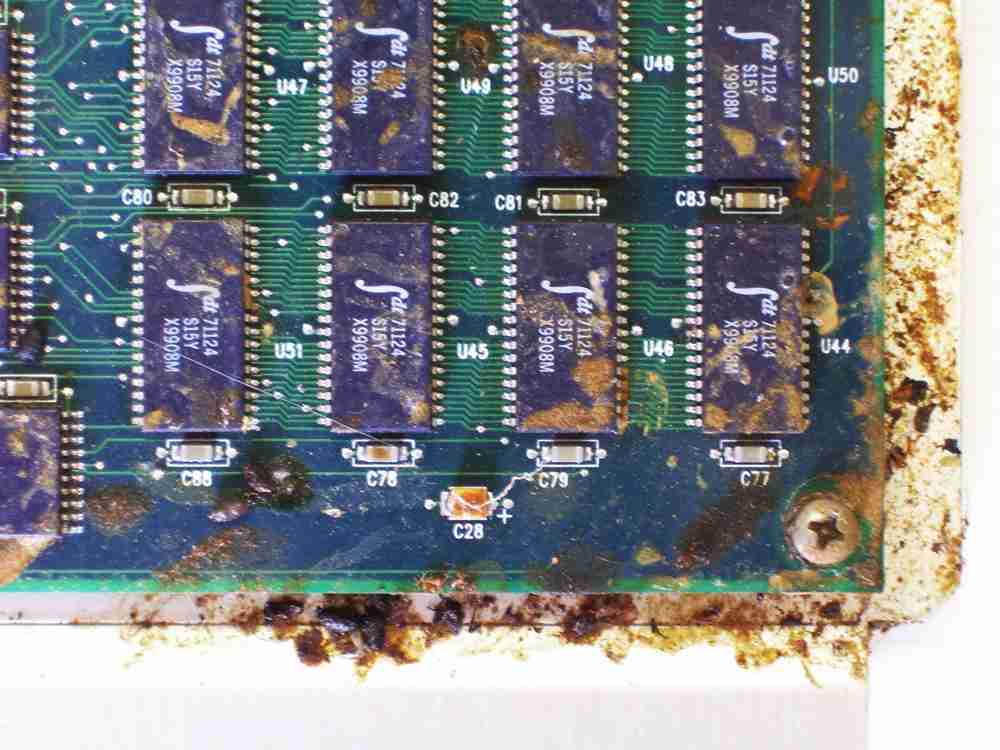
... and a closeup of the bottom right corner.
(click
on any of these photos for an enlargement)
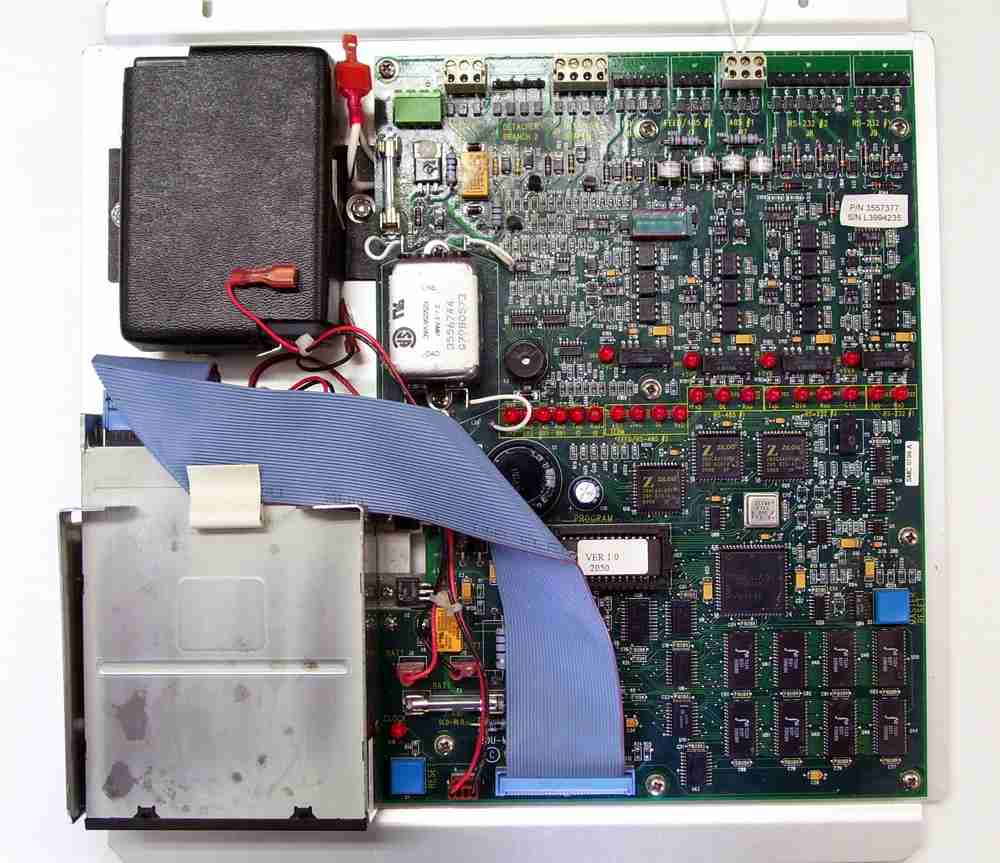
Here's a photo
of the same 2050 ... once repaired.
The
only evidence of the damage are the stains on the top of the floppy
drive unit (bottom left hand corner).
This
is really a testamont to the quality of the build of these units and
the protective coating over all the boards that Boumatic build.
A household PC or any normal electronics wouldn't have survived even 5%
of the c&@p that was thrown at this one. :)
The
coating is an absolute pain to work with ... measuring
components and trying to resolder through ... but I think
these photos are proof that the stuff works superbly even in the worst
of environments.
We are able to renew this coating on the areas we work on, to provide
continued long term protection for the electronics.